آشنایی با انواع روش اسید شویی
اسید شویی یک فرایند سطح سازی فلز است که برای حذف ناخالصیها مانند لکهها، آلودگیهای غیر آلی، زنگ زدگی یا رسوب از سطح فلزات آهنی، مس، فلزات گرانبها و آلیاژهای آلومینیومی انجام میشود. یک محلول به نام pickle liquor که معمولا حاوی اسید است، برای حذف ناخالصیهای سطحی مورد استفاده قرار میگیرد. ازین فرایند معمولا در فرایندهای مختلف تولید فولاد، از بین بردن رسوب یا تمیز کردن فولاد استفاده میشود.
اسیدشویی به حذف یک لایه نازک فلز از سطح فولاد ضدزنگ گفته میشود. معمولا برای اسیدشویی فولاد ضدزنگ از مخلوطی از اسید نیتریک و هیدروفلوئوریک اسید استفاده میشود. اسیدشویی فرایندی است که برای حذف لایههای تغییر رنگ داده شده توسط جوشکاری از سطح فولاد ضدزنگ استفاده میشود، جایی که میزان کروم سطحی فولاد کاهش یافته است.
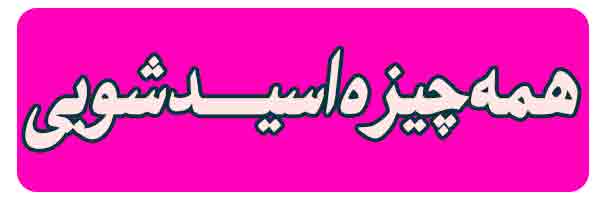
چند روش اسید شویی وجود دارد؟
برای انجام عملیات شستشو با اسید روش های مختلفی را می توان بکار برد که مهم ترین آنها استفاده از حمام اسیدی، اسپری کردن و یا استفاده از قلمو است. در روش حمام که به اسم روش غوطه وری نیز شناخته می شود، فلز مورد نظر به داخل حمام اسیدی فرو برده می شود. در روش های دیگر نیز با استفاده از اسپری کردن و یا قلمو محلول اسیدی بر روی سطح مورد نظر اعمال می شود ، این روش برای فلزاتی که به صورت موضعی نیاز به تمیزکاری دارند بیشتر مورد استفاده قرار می گیرد. در مواردی مانند تولید فولاد که همواره لایه اس از اکسید بر روی سطح شکل می گیرد، استفاده از روش غوطه وری معمول تر است.
- اسید شویی استخر
- اسید شویی فولاد
- اسید شویی نمای ساختمان
- اسیدشویی به روش قلم مو
در این روش نیز مانند روش بالا مایع اسیدی را با استفاده از قلم مو بر روی سطح فلز مورد نظر اعمال می کنند و مدت زمان مشخصی صبر می کنند تا تمام آلودگی ها از بین بروند، سپس سطح فلز با آب شستشو داده می شود. البته این نکته لازم به ذکر است که از این دو روش اخیر برای فلزاتی استفاده می کنند که به صورت موضعی نیاز است که از آلودگی پاک شوند و در واقع برای پروژه های عظیم صنعتی کاربرد ندارد.
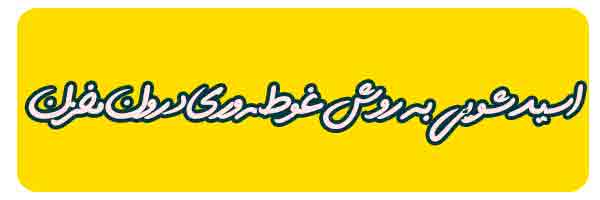
-
اسیدشویی به روش غوطهوری درون مخزن
در این روش قطعات فلزی را در حوضچه های مخصوص برای مدت زمان معین در مایع اسیدی غوطه ور می کنند و عملیات زدودن آلودگی ها از زمان غوطه ورسازی شروع می شود. بعد از اتمام زمان معین، فلزات را به حوضچه های دیگری برای شستشو با آب خالص منتقل می گردد.
شستن فلزات با آب خالص باعث از بین رفتن اسیدهای باقی مانده روی فلز و همچنین برخی از آلودگی هایی می شود که همچنان روی سطح فلز وجود دارند.
باید در انجام فرآیند اسید شویی فلزات، به مدت زمان غوطه ورسازی در اسید دقت شود. اگر از مایع اسیدی مناسب و به میزان مناسب برای عملیات اسید شویی استفاده شود، قطعاً بیشترین بازدهی را با کمترین میزان خوردگی فلز با اسید خواهیم داشت.
مطالعه کنید: برای خرید استات سدیم کلیک کینید.
2.اسید شویی به روش اسپری بر روی سطوح
یکی از مهمترین کاربردهای این فرآیند استفاده از آن در تولید نورد است. عموما برای این کار از اسید نیتریک و یا سولفوریک استفاده می شود . در ادامه به مزایا و معایب استفاده از هرکدام از این اسیدها اشاره شده است.
3. اسید شویی فلزات با استفاده از حوضچه ها و حمام اسید
روش استفاده از حوضچه ها و حمام اسید را در واقع روش غوطه ورسازی می نامند. در این فرآیند، قطعات فلزی را در حوضچه های مخصوص برای مدت زمان معین در مایع اسیدی غوطه ور می کنند و عملیات زدودن آلودگی ها از زمان غوطه ورسازی شروع می شود. بعد از اتمام زمان معین، فلزات را به حوضچه های دیگری برای شستشو با آب خالص منتقل می گردد. شستن فلزات با آب خالص باعث از بین رفتن اسیدهای باقی مانده روی فلز و همچنین برخی از آلودگی هایی می شود که همچنان روی سطح فلز وجود دارند. باید در انجام فرآیند اسید شویی فلزات، به مدت زمان غوطه ورسازی در اسید دقت شود. اگر از مایع اسیدی مناسب و به میزان مناسب برای عملیات اسید شویی استفاده شود، قطعا بیشترین بازدهی را با کمترین میزان خوردگی فلز با اسید خواهیم داشت.
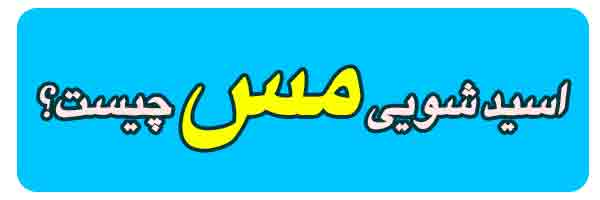
1. اسید شویی مس
این اسید به عنوان یکی از اسیدهای صنعتی استفاده میشود و در صنایع مختلف بهویژه صنایع مرتبط با فلزات، به خصوص صنایع مس، استفاده میشود.
2. اسید شویی فسفریک
اسید فسفریک به عنوان یک اسید نسبتا نرم، برای شستشوی و تمیزکاری سطوح فلزی مختلف مانند مس و آلیاژهای مسی استفاده میشود. همچنین، در فرآیندهایی که نیاز به اسیدی با خواص خاص مانند انحلال و رفع اکسیداسیون دارند، مورد استفاده قرار میگیرد.
همچنین، این اسید در تولید فسفات و سوپر فسفات نیز مورد استفاده قرار میگیرد. از طرف دیگر، برای تولید سمادهای فسفاته نیز بهره برده میشود.
3. اسید شویی آهن
اسید شویی آهن معمولا به اسید هیدروکلریک اشاره دارد، که با فرمول HCl شناخته میشود. این اسید یکی از اسیدهای قوی است و به عنوان ماده شویی و تمیزکاری در صنایع مختلف به کار میرود. در مورد آهن، از اسید هیدروکلریک برای تمیزکاری، از بین بردن زنگ زدگی، از بین بردن اکسیداسیون و رسوبهای فلزی استفاده میشود.
4. اسید شویی کلریدریک
همچنین، اسید کلریدریک به عنوان یکی از مواد شیمیایی مهم در صنعت فلزات برای تولید محصولات فلزی از جمله آهن و فولاد نیز استفاده میشود. در فرآیندهایی مانند گالوانیزهکردن (رسوب کردن لایههای رسی از روی آهن) نیز بهرهبرداری از اسید هیدروکلریک رایج است.
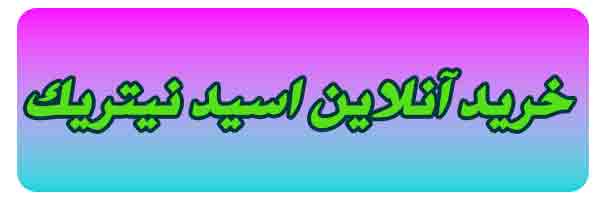
فرآیند اسید شویی با اسید نیتریک چگونه است؟
مزایا
- نفوذ کمتر هیدروژن
- کاهش هزینه های گرمایشی
- حذف scale ها در مقیاس بزرگ
- رسوب کمتر نمک آهن بر روی سطح شسته شده
معایب
- خورندگی بیشتری برای تجهیزات دارد.
- سیستم های بزیابی اسید گران قیمت هستند.
- هزینه بالاتر دفع در مقایسه با اسید سولفوریک.
- در صورت تجاوز دما از دمای محیط، کف تشکیل می شود.
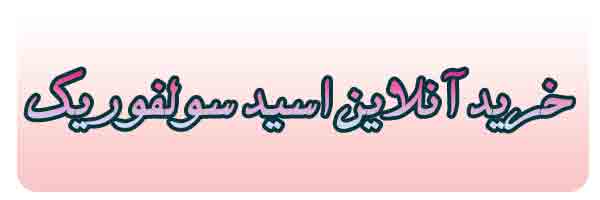
اسید شویی با اسید سولفوریک
مزایا
- بازیابی سولفات آهن آسان است.
- اسید می تواند بسیار سریعتر بازیابی شود.
- سرعت فرآیند را می توان با دما کنترل کرد.
- افزایش دما باعث کاهش غلظت اسید می گردد.
معایب
- حمله بیشتر اسید به فلز پایه
- نفوذ بیشتر هیدروژن به داخل فولاد
- محلول اسیدی باید حرارت داده شود.
- باقی مانده های اسیدشویی چسپندگی بیشتری دارند.
هدف از اسید شویی فلزات چیست؟
به دلیل انجام عملیات های متنوع بر روی فلزات در صنایع بسیار امر بیعی است که روی سطح فلز را یک لایه بپوشاند که حتما باید برای انجام مراحل بعدی همچون رنگ کاری، فلز کاملا سطح تمیز و عاری از هرگونه آلودگی داشته باشد.
که بطور کلی می توان گفت به دو دلیل اصلی اسید شویی در فلزات انجام می شود:
1 – جدا شدن لایه های اکسید از سطح، ورق اسید شویی دارای ظاهری بهتر و سطحی با کیفیت مرغوب تر خواهد شد.
2 – پوسته های اکسیدی روی سطح ورق اسیدشویی سخت و ضد سایش می باشند. بنابراین در صورتی که ورق ها بدون اسیدشویی وارد مرحله نورد سرد شوند موجب افزایش استهلاک غلتک های نورد می گردند. از این رو ورق می بایست پیش از ورود به مرحله نورد سرد تحت عملیات اسیدشویی قرار گیرد.
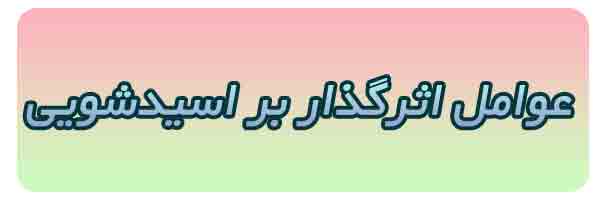
چه عواملی بر اسید شویی تاثیر گذار است؟
1.نوع اکسید موجود روی فلز
2.میزان چسبندگی اکسید بر روی فلز
3.ضخامت لایه اکسید شده از فلز
4.نوع محلول اسیدی مورد استفاده
5.دما و غلظت محلول اسیدی مورد استفاده
6.مدت زمان قرارگیری قطعه فلزی در محلول اسیدی
7.سرعت چرخش محلول اسیدی در حوضچه مخصوص
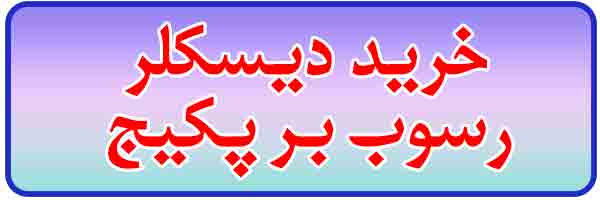
دستورالعمل استاندارد فرآیند اسید شویی
اسیدشویی یکی از متداول ترین فرآیندهای صنعتی است. این فرایند در کارهای آبکاری کوچک، کارخانه های اتومبیل سازی، کارخانه های تولید فولاد و هر کارخانه ای که کار آن شامل استفاده از یک پوشش برای فلزی پایه باشد دیده می شود. اسیدشویی فرآیندی است که از طریق آن اکسیدها و جرم های یک سطح فلزی به طریق شیمیایی و با غوطه وری ساختن آن در یک اسید معدنی رقیق که معمولا اسید سولفوریک و یا هیدروکلریک است، برطرف می شود.
انجام تمام مراحل این فرآیند به صورت صحیح و تحت استاندارد از اهمیت ویژه ای برخوردار است. چرا که در صورت عدم رعایت استانداردهای آن و عدم تکمیل مراحل اسید شویی محصول نهایی بازدهی که باید را به مصرف کننده نمی دهد. پس خرید شما از تولیدکننده مطمئن تضمین کننده خرید محصول با کیفت می باشد. بر همین اساس ورق اسید شویی فولاد مبارکه اصفهان می تواند انتخاب خوبی برای شما باشد که برای دریافت اطلاعات این محصول می توانید به لینک مربوطه مراجعه نمائید.
در واقع اسید شویی فلزات به روندی گفته می شود که طی آن، تمام آلودگی ها، پوسته های اسیدی و زنگ زدگی ها که روی سطح فلزات تولید شده قرار دارد، طی عملیاتی با استفاده از مایعی اسیدی که به نام مایع اسید شویی معروف است، زدوده می شود و فلز برای استفاده در مراحل بعدی کاملاً تمیز می گردد. اسیدی که برای اسید شویی فلزات مورد استفاده قرار می گیرد معمولا هیدروکلریک اسید است. فلزات با مقاومت بالا را با اسیدهای قوی تر و در دو مرحله اسید شویی می کنند.
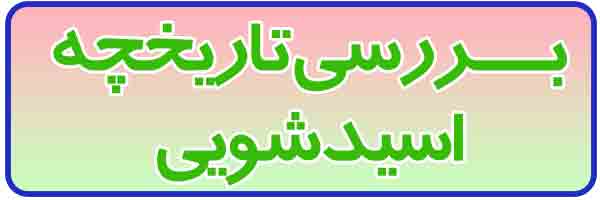
تاریخچه استفاده از اسید در فرایند اسید شویی
اسیدشویی تقریبا تا این اواخر از نظر فنی تغییر چندانی نکرده بود، هر چند در حالی که قبلا تنها تقریبا از اسیدشویی با اسید سولفوریک استفاده می شد، اینک تمایلی وجود دارد که در خطوط اسیدشویی پیوسته از اسیدشویی با اسید کلریدریک استفاده شود و باید توجه بیشتری به مشکلات تخلیه پساب اسیدشویی یا بازیابی اسید مبذول گردد.
نوع عملیات اسیدشویی عمدتا بستگی به محصولی دارد که قرار است تمیز شود، معمولا در اسیدشویی از اسیدهایی مانند اسید سولفوریک، هیدروکلریک ، فسفریک، هیدروفلوریک و نیتریک به تنهایی یا به صورت ترکیب های گوناگون استفاده می کردند. تاکنون برای اسیدشویی آلیاژهای فولادی کربن دار، اسید سولفوریک بیشترین استفاده را داشته است همراه با اسید هیدروکلریک که در رده پس از آن به میزان روز افزونی بیشتر مورد استفاده می باشد.
یکی از کاربردهای بسیار زیاد هیدروکلریدریک اسید تولیدی در سطح جهان، در صنایع فولادسازی است. مثلا در کشور کانادا بیش از 26 درصد از کل هیدروکلریدریک اسید تولیدی به مصرف واحد اسیدشویی می رسد. یعنی از 113 تن هیدروکلریدریک اسید تولیدی در حدود 30 تن در صنعت اسیدشویی آهن و فولاد مصرف می شود.
زمان مناسب برای انجام عملیات اسید شویی و روغن کاری فلزات
عملیات اسید شویی و روغن کاری فلزات را معمولاً در آخرین مرحله از عملیات روی فلزات انجام می دهند. زیرا اگر مراحل دیگری بعد از این عملیات انجام شود، احتمال این وجود دارد که دوباره تجهیزات مختلف مانند غلتک ها و غیره آلودگی را بر روی سطح فلز منتقل کنند. در این مورد یک استثنا وجود دارد و آن وقتی است که بنابر شرایط مورد نظر و پس از قرارگیری تحت عملیات نورد گرم، نیاز باشد که فلز عملیات نورد سرد را نیز تحمل کند. در این شرایط، لازم و ضروری است که نورد سرد روی فلزی انجام شود که تمام آلودگی های آن توسط فرآیندهای اسید شویی و روغن کاری فلزات از بین رفته باشد.
فلزات مختلفی نیاز به اسید شویی و روغن کاری دارند که برخی از آن ها عبارتند از:
گاهی اوقات آلیاژهای آلومینیوم برای مصارف خاصی نیاز به اسید شویی و روغن کاری دارند.
اکثر آلیاژهای فولاد، مخصوصا فولاد ضد زنگ برای این که کارایی بهتری داشته باشند به عملیات اسید شویی و روغنکاری نیاز دارند ولی باید دقت شود که هر چه میزان
عناصر آلیاژی در فولاد بالاتر باشد، نیاز به استفاده از اسید قوی تری است.
به طور کلی مراحل نورد به صورت زیر می باشد:
در اولین مرحله نورد با استفاده از روش ریخته گری پیوسته تختال هایی به طول 4.5 تا 10 متر و ضخامت 20 سانتی متر تولید می گردند. پس از ریخته گری تختال به واحد خنک کننده منتقل می گردد تا دمای آن به دمای محیط نزدیک شود.
هدف از نورد گرم تولید ورق با ابعاد معین، شکل دلخواه، خواص مطلوب و صافی سطح مورد نیاز از یک تختال با ابعاد مشخص می باشد. دلیل اصلی استفاده از نورد گرم مقاومت کم فولاد در مقابل تغییر شکل در درجه حرارت بالاست. فولاد کم کربن در دمای بالاتر از 890 درجه سانتی گراد در فاز آستنیت قرار دارد. در صورتی که تمامی تغییرات در فاز آستنیت انجام شود می توان گفت که فرایند نورد به صورت همگن خواهد بود. با توجه به اینکه دمای خروجی تختال از کوره پیش گرمکن به تلفات حرارتی حین عملیات نورد وابسته است، بنابراین تختال می بایست در کوره به دمایی برسد تا با دمایی بیش از 890 درجه سانتی گراد از آخرین مرحله نورد نهایی خارج شود.
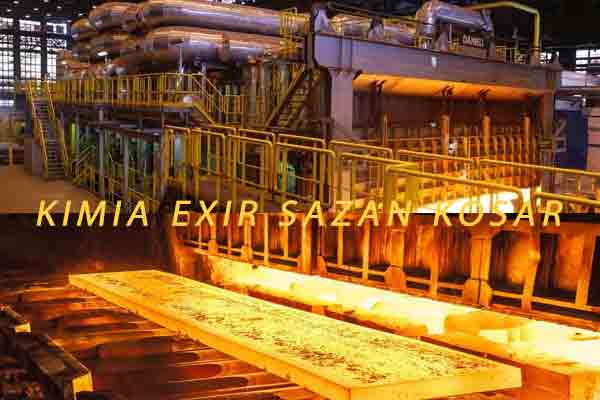
در کوره پیش گرم تختال با نرخ معین حرارت داده می شود تا به دمای مورد نیاز در نورد گرم برسد. در طول این مدت برای جلوگیری از ناهمگونی در تغییر شکل توزیع دما در تمامی نقاط تختال می بایست به گونه ای یکنواخت باشد. بدین منظور از کوره های هم دماساز استفاده می شود تا دمای تختال در هنگام خروج از کوره به گونه ای یکنواخت در آید. این دما به ابعاد تختال، شرایط نورد، نوع فولاد، تعداد مراحل نورد، دمای ورق در مرحله پایانی و عوامل دیگر بستگی دارد. این دما برای فولاد کم کربن در حدود 1300 درجه سانتی گراد می باشد.
نکته مهم در طی این مرحله مدت زمان نگهداری تختال در کوره پیش گرمکن می باشد زیرا طولانی شدن این زمان علاوه بر اتلاف انرژی باعث خوردگی بیش از اندازه تختال و حتی سوزاندن کربن موجود در فولاد می گردد. تختال پس از خروج از کوره پیش گرمکن پوسته زدایی می گردد تا قابلیت ورود به مراحل بعدی نورد را داشته باشد.
به منظور تولید ورق لازم است تا در ابتدا ضخامت تختال ریخته گری شده در طی 2 تا 3 مرحله نورد مقدماتی کاهش یابد. ضخامت تختال در این مرحله از 250 الی 350 میلی متر به 25 الی 35 میلی متر کاهش می یابد. این عملیات عموما توسط قفسه های رفت و برگشتی یونیورسال انجام می گیرد. پس از خروج تختال از مرحله نورد مقدماتی تختال مجددا پوسته زدایی می گردد. دما در این مرحله تا حدود 1100 درجه سانتی گراد کاهش می یابد.
در کارخانه نورد گرم با آرایش همزمان برای هماهنگی و جلوگیری از برخورد تختال های عبوری، از یک میز انتقال در فاصله میان مراحل نورد مقدماتی و نهایی استفاده می شود. استفاده از این میز باعث هماهنگ شدن سرعت بالای تختال در هنگام نورد مقدماتی و سرعت پایین آن در مرحله قیچی و اولین مرحله نورد نهایی می شود.
با توجه به طول زیاد میز انتقال اتلاف حرارت قابل توجهی از سطح تختال صورت می گیرد که باعث ناهمگونی دما در تختال و در نتیجه کاهش مرغوبیت فولاد تولیدی، افزایش استهلاک قطعات، افزایش هزینه سوخت، کاهش راندمان کارخانه و افزایش آلودگی محیط زیست می گردد. با توجه به این مساله اتلاف حرارت در چند دهه اخیر مورد توجه محققان قرار گرفته است. آن ها روش های مختلف را برای کاهش اتلاف انرژی در فاصله نورد مقدماتی و نهایی به کار گرفته اند. تختال پس از عبور از میز انتقال وارد مرحله نورد نهایی می شود.
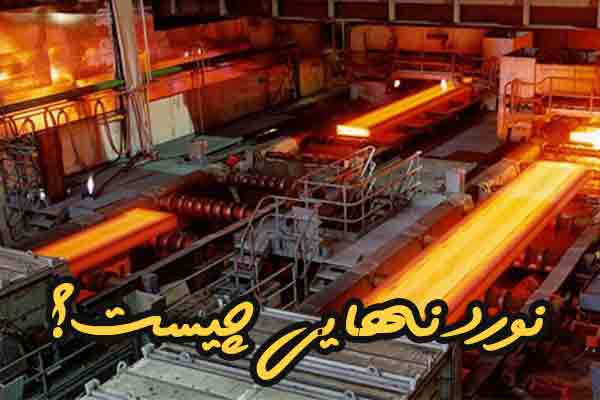
تختال عبوری از میز انتقال به منظور تولید ورق به سمت قفسه های نورد نهایی فرستاده می شود. معمولا این خط از 6 تا 7 قفسه تشکیل شده است که در آن ضخامت ورق به 1.8 تا 3 میلی متر کاهش می یابد. دمای ورق در خروج از نورد نهایی تا حدود 900 درجه سانتی گراد کاهش می یابد.
پس از اتمام عملیات نورد نهایی ورق به واحد خنک کاری وارد می گردد. عملیات خنک کاری به این دلیل بر روی ورق انجام می گیرد تا در هنگام کلاف پیچی لایه های ورق به یکدیگر جوش نخورند. کم کردن دمای ورق با پاشیدن جریان آب در قسمت سردکننده انجام می گیرد تا درجه حرارت ورق به 650 درجه سانتی گراد کاهش یابد. در این دما ورق توسط دستگاه کلاف پیچ به صورت کلاف های استوانه ای در می آید.
کلاف ها توسط سیستم حمل کلاف به انبار منتقل و تا رسیدن به دمای محیط در آن نگهداری می شوند.
پس از آن کلاف ها به واحد تکمیل نورد گرم یا نورد سرد تحویل می گردند.
مرحله بعد تولید ورق اسیدشویی می باشد که به طور مفصل در بالا ذکر گردید
به دلیل کاهش بیشتر ضخامت و دستیابی به خواص مکانیکی بهینه، ورق های تولید شده در واحد نورد گرم پس از اسیدشویی تحت عملیات نورد سرد قرار می گیرند. نورد سرد متوالی مرسوم به تاندم به صورت 4 تا 6 قفسه ای و اخیرا به صورت رفت و برگشتی 2 تا 3 قفسه ای انجام می گیرد. در فرایند نورد سرد ضخامت ورق بین 25 تا 90 درصد کاهش می یابد. ورق های تولید شده با ضخامت های گوناگون 0.1 تا 6 میلی متر به شکل کلاف یا ورق تهیه می شوند.
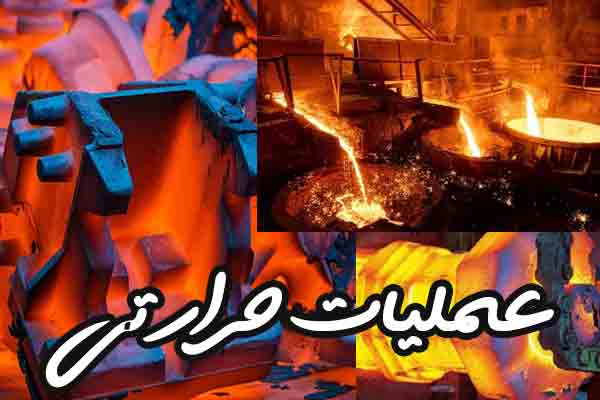
ساختار نهایی فولاد در ویژگی های فیزیکی و مکانیکی آن ها تاثیر به سزایی دارد. بنابراین برای دستیابی به خواص مکانیکی بهینه و آرایش یکنواخت ورق، کلاف تحت عملیات حرارتی قرار می گیرد. کلاف ها به صورت دو یا سه تایی روی یکدیگر قرار گرفته و یک پوسته استوانه ای شکل روی آن ها قرار می گیرد. سپس کلاف ها تحت عملیات حرارتی قرار می گیرند. پس از حرارت دهی کلاف ها به آرامی سرد می گردند.
هدف از نورد پوسته ای ایجاد کار اندک در ورق می باشد تا در آن چقرمگی و مقاومت مکانیکی افزایش یابد. در این مرحله تغییر شکل پلاستیک بسیار کمی بر ورق اعمال می گردد. این موضوع به همراه کنترل دقیق ضخامت موجب می شود تا صافی سطح ورق افزایش یابد و ناصافی ایجاد شده در ورق در طی مراحل قبل به حداقل ممکن برسد.
چرا به این فرآیند اسید شویی میگویند؟
فرآیند اسید شویی شامل فرو بردن فلز در محلول برای حذف رسوب و ناخالصیهای سطحی آن است. محلول مورد استفاده pickle liquor نامیده میشود که یک نوع محلول اسیدی است. از این رو فرآیند فرو بردن فلز در این محلول اسیدی به اسیدشویی معروف است.
در فرآیند اسید شویی چه اتفاقی می افتد؟
در این فرآیند، اکسید آهنی که در دمای بالا ایجاد شده، طی یک فرآیند دیگر حرف میشود. پوسته از لحاظ شیمیایی بسیار شبیه به زنگ زدگی است، چرا که پوسته هم از پیوند آهن و اکسیژن با آرایش مولکولی متفاوت تشکیل شده است. همانند زنگ زدگی، پوسته نیز بر روی سطح فولاد ایجاد میشود، یعنی جایی که آهن در معرض هوا قرار میگیرد.
اما این پوسته ها معمولا یک تفاوت بزرگ با اکسید آهن دارند و آن این است که پوسته در دمای بالا تشکیل میشود. با گذر زمان، این پوسته عمق بیشتری در فولاد پیدا میکند و سرعت رشد آن نیز با افزایش دما بهسرعت افزایش پیدا میکند. برای مثال، تختالها در دستگاه پرداخت نورد گرم زمانی که از کوره پیش گرم خارج میشوند، ضخامت یک لایه از پوسته آنها به بیش از 1/8 اینچ میرسد.
بهطور معمول لایه عادی پوسته، یا پوشش پوسته، که با اسید شستشو میشود، ضخامتی کمتر از یک هزارم اینچ و ظاهری به رنگ خاکستری مات دارد.
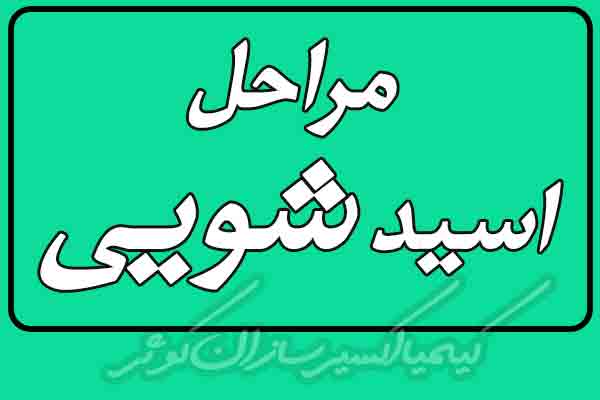
مراحل کلی فرآیند اسید شویی چیست؟
تهیه محلول اسیدی با ترکیبات و غلظت مورد نیاز برای نوع فلز و آلایندههای موجود. انتخاب اسید و غلظت آن بسته به نوع فلز و نوع آلایش متفاوت است.
قطعات فلزی را در محلول اسیدی قرار دهید یا با استفاده از برس و اسفنج اسید را روی سطح فلز پخش کنید. این کار باعث حذف آلایندهها، زنگ زدگی و رسوبات فلزی میشود.
پس از مدت زمان مناسب، فلزات را با آب داغ یا آبکشی کامل کنید تا اسید را از روی سطح پاک کنید.
قطعات را بهطور کامل خشک کنید تا از ایجاد زنگزدگی مجدد جلوگیری شود.
پس از تمیزکاری، استفاده از روشهایی مانند پوششدهی با روغنهای ضدزنگ یا پوششهای حفاظتی بر روی سطوح فلزی را پیشنهاد میکنیم تا از زنگزدگی مجدد جلوگیری شود.